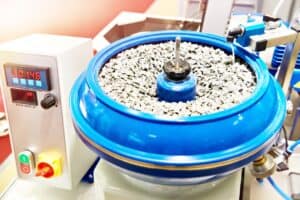
Exploring the Best Finishing Solutions: Vibratory Bowls, Tub Finishers, and Centrifugal Systems
Key differences between the three popular finishing machine styles: vibratory bowl finishers, vibratory tub finishers, and centrifugal finishing systems. Each machine type offers unique advantages depending on the specific needs of your production process, such as part size, material, and the desired finish.